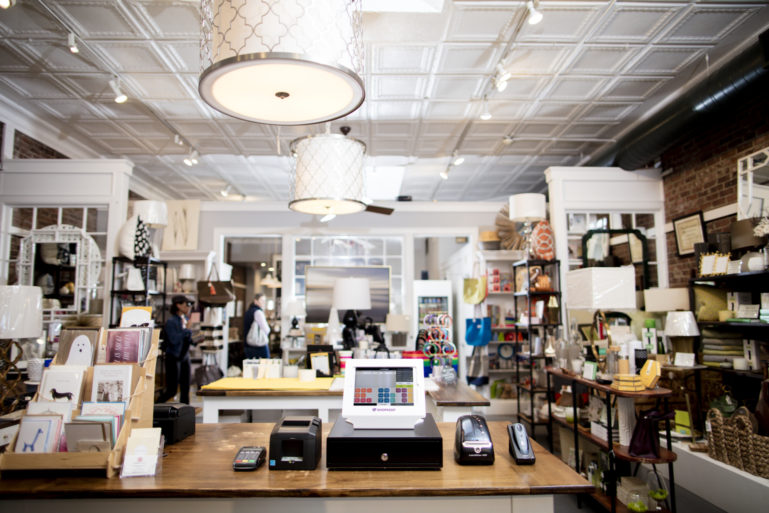
Getting Started with Simple Inventory Control Procedures
Adequate inventory control procedures are not only essential to the overall operations of your store, but also to the long-term health of your business.
One key to good inventory control is making sure that you have items available to be sold to your customers. This might seem simple, but lackadaisical inventory control practices can lead to inexact quantities on hand, meaning items may not be available to customers when needed. It is also important in regards to loss prevention and the overall value of your business. Let’s take a look at a few inventory control procedures to help keep your stock accurate and organized.
Know What You Have On Hand
To begin with, know how much or how many of your inventory items you have available to sell at any given moment. Knowing your inventory levels is key to making sure that your merchandise is readily available to your customers. There are a few different ways in which this can be accomplished.
Physical Inventory Counts
One reliable method of keeping your inventory control in check is to complete a physical inventory count. Taking a physical Inventory is the act of counting each item in your inventory and is a great way to accurately keep track of your entire inventory. Because this procedure includes physically counting each item — opposed to relying on the deductions of a computer — it ensures that stock totals are correct. To be blunt, it’s one of the most accurate ways available of monitoring inventory. How often should a physical inventory be conducted you ask? It all depends on the number of inventory items your business carries. Depending on this number, you can decide whether to conduct a count quarterly, bi-quarterly or yearly.
Cycle Counting
Cycle counting is also an excellent inventory control procedure for keeping track of your stock levels — that is, in between your physical inventory counts. Cycle counting involves separating inventory items into groups. Once separated, one group of items is counted per day, with the goal of working through a count of your entire inventory. Groups can be categorized by item type, location at your business, or by more selective methods such as seasonal best sellers and/or price brackets. When counting by item type, a selected type of item is counted on that day. When counting by location, a particular section of your business is counted. For more selective inventory methods, groups can be separated by margin or total sales.
ABC analysis is one type of selective cycle counting. It ranks items into three major groups, ‘A’, ‘B’, and ‘C’. They are ranked by level of importance, ‘A’ being the most crucial to your business, such as higher margin items or top selling items. Because of level A’s value to your business, these are the items that you’ll want to keep track of more rigorously. It can be items with high values or top selling items.
SEE ALSO: How to Easily Determine Your Inventory Turnover Ratio
Keep Track of When An Item is Sold
For proper inventory control, it’s also critical to keep track of sales. Traditionally, businesses used paper lists or spreadsheets to keep track of inventory levels. But as you can imagine, this created a large margin of error. For more accurate inventory control and management, we recommend using more reliable tracking methods. Setting up your inventory management by using a cloud-based POS system, can assist you in methodically maintaining your inventory with real-time updates. When an item is sold, returned, or brought into your store to restock, the counts are updated across all systems the moment that the change is made. Additionally, they prevent inventory data from being lost as a result of lost or damaged software or hardware.
When organizing your inventory with a POS system, there are a few things to keep in mind. Be sure to use any available adjustment tools. In addition, don’t forget to remove items from your inventory for other reasons besides sales. Remember, if an item has been designated for a display or is perishable and has spoiled, they should also be removed from the count for up-to-date and correct stock levels.
Enter Counts Diligently
Along with ensuring that inventory counts are correct, entering costs and monitoring sales reports can help you make informed inventory decisions about whether certain items are worth carrying. Determining whether the cost outweighed the benefit on items is made easier with the ability to automatically calculate margins.
With your inventory counted and entered into the system accurately, this will reduce errors at the register when your inventory is moving quickly out the door. Improper entry can negatively affect inventory counts. When selling items, be sure that similarly named items are not being confused. We suggest using UPCs and scanning items when completing sales at the register. In addition, when ringing up items, make sure that every item is accounted for before it is placed in a bag. The honest mistake of not ringing up an item can lead to inaccurate inventory counts.
As we’ve stressed in this post, accuracy is key to successful inventory control. Throughout the process, holding yourself and your staff to the highest standards is of the utmost importance. Now that you have learned some practices to help you get started, apply a few of our tips and tricks to help streamline operations in your store. Have additional suggestions that we haven’t mentioned? Let us know by commenting below!
Want to try ShopKeep for yourself?
Just answer a few easy questions.
Need help finding the right point of sale?
Just complete the form. We’ll call you right back to explain how ShopKeep can work for you.
Hit the ground running.Sprinting, in fact!
Read our free, comprehensive guide, Small Business 101, to learn all you need to know about starting a thriving business.